Booster Module BMS
To get a higher flow rate than one module, you can connect multiple modules in parallel. The total flow rate is the sum of the flow rates of each module. The pressure does not change and is equal to the pressure of one pump.
You should use a flush pump to prevent corrosion when the booster system pumps seawater or aggressive water in a reverse osmosis system or similar applications. You should flush the system with clean fresh water until the whole system has a salinity of less than 1000 ppm TDS.
For seawater and brackish water reverse osmosis filtration applications, the BMS series offers a new and innovative range of booster modules pumps. A permanent magnet motor and VFD power a directly coupled pump, which is one of the many material selection options it features. Moreover, super duplex and stainless steel make up all the critical components in this series that touch water.
The pumps can only handle thin liquids that are not explosive and do not have solid particles or fibre. The liquid should not damage the pump materials chemically. If you are unsure, please contact US. The pumps cannot work with liquids that have substances like soap that lower the surface tension. You should use a bypass to divert the liquid around the pumps if you clean the system with this kind of detergent. The motors may need more power than the standard output if the pumped liquid is denser or thicker than water. BMS has booster systems work well with brackish water and seawater. The liquid shouldn’t be hotter than 40 °C (104 °F).
Automatic Control Devices
You should use flow and pressure control devices to prevent the pumps from running dry.
The pressure switch on the inlet side matches the expected inlet pressure. The pump will stop and an alarm will sound if the pressure drops below 1 bar (14.5 psi).
You should also use flow switches on all the system’s outlet connections. These switches will stop the system if the flow rate falls below the minimum level.
The control devices keep the inlet pressure right.
The flow switch cutting-in has a minimum time delay that matches the system’s maximum starting frequency.
Automatic Safety Devices
To protect the pump, the system must include the following safety devices.
- A flow switch and/or a low-pressure switch that lubricates the thrust bearing and pump bearings by ensuring a minimum water flow
- A flowmeter on each outlet pipe
- A low-pressure switch on the booster system inlet that matches the estimated inlet pressure. If the pressure drops below 1 bar (14.5 psi), the switch triggers an alarm and stops the pump
- A high-pressure switch on the outlet pipe that stops the pump when it reaches a preset maximum pressure
- These safety devices guarantee a proper inlet pressure and a sufficient flow for lubrication
- The flow switch has a minimum time delay that corresponds to the system’s maximum starting frequency
Booster Module Performance Range
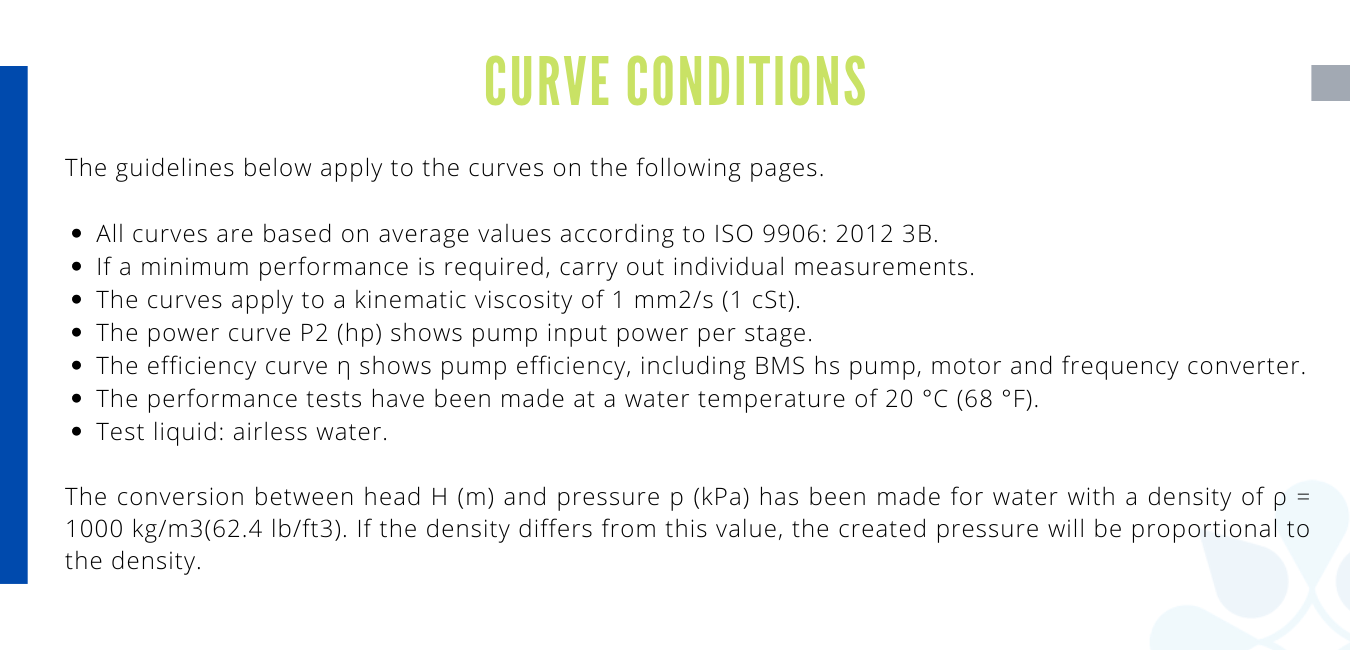
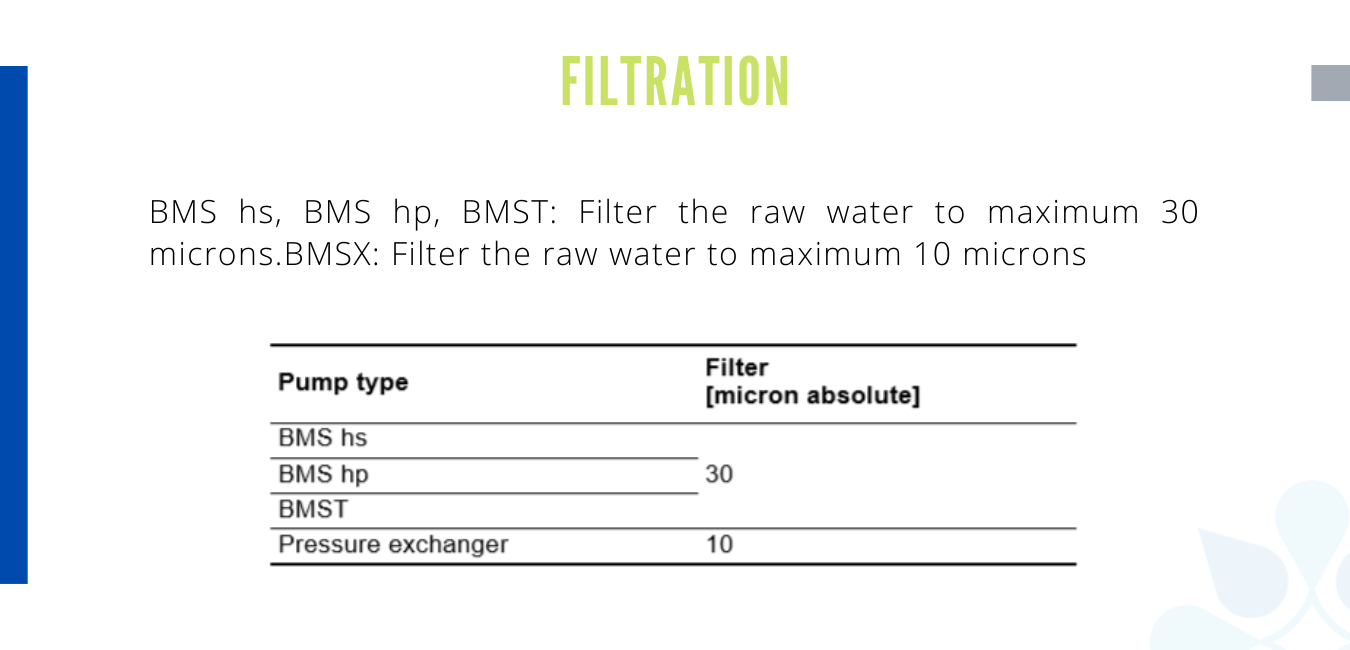
Get Booster Module BMS From PT GLS
PT Gapura Liqua Solutions reflect our commitment to control the product quality by working closely with our strategic business partners, mostly leading components manufacturing firms in the field of water treatment, waste water treatment, desalination, and resources recovery.
You will guarantee product originality, advisory for your water system, and taking care by our skilled engineer to meet your business goals. Contact us now!